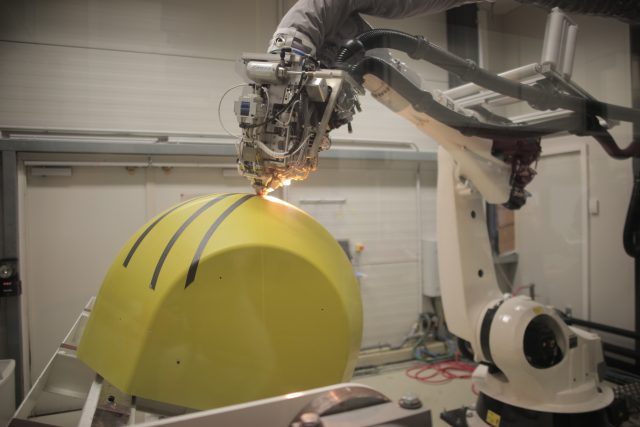
MUNICH—As a perennial fan of "How It’s Made" videos, my visit last month to GE’s Global Research Center in Munich was particularly fascinating. Although the campus is not involved with any actual large-scale manufacturing, the scientists and researchers there do focus on finding ways to take manufacturing processes and make them better. There were endless miniature manufacturing nooks and crannies that we got to poke our noses into over the course of our week.
I came away fixated on carbon fiber. It’s most famously used as a lightweight, high-strength construction material in exotic cars and aircraft, but it’s becoming downright common these days. Today carbon fiber is in bicycles and golf clubs, and you can even get yourself a carbon fiber wallet if you’re so inclined. But its growing presence in everyday life belies its beauty and complexity—there’s nothing common about this increasingly common material.
It takes a lot to make a composite
Carbon fiber is properly described as a "composite material," a term that is used to describe any substance with multiple components that combine in interesting ways to produce a material with complex, desirable properties. Most of our time on the GE campus was spent in the center’s composite manufacturing lab, and we were surrounded by tons of different composite materials, from glass to metals—but carbon fiber was the thing we focused on.
Carbon fiber’s standout properties, and the reason that you see it showing up in body panels of cars and in jet turbines, is that as a finished material it can be made both much stronger and much lighter than equivalently sized metal parts. "Stronger" here refers to a multitude of different measurement. For example, as explained here, carbon fiber has a tensile strength (that is, it resists being stretched) roughly four times greater than steel and eight times greater than aluminum. It is also stiffer (it resists bending) than steel or aluminum by a significant amount. These gains in strength are accompanied by a drastic reduction in weight: typically, a carbon fiber part weighs only a third as much as a steel part of the same volume.
As a composite material, carbon fiber derives its stiffness and lightness from two things: first are the components, which are strands of spun carbon filament, thinner than a human hair, and some form of glue or epoxy to bind the carbon into a shape. The second thing that gives the composite its strength is the chemical change wrought by combining the two materials and then letting them blend, or more properly, letting the epoxy "cure." Carbon fiber manufacturing processes differ depending on what kind of shape or part you’re making, but the manufacturing methods all have "thread and glue" in common.
To make a part from carbon fiber, typically you need a mold of some sort, against which carbon fiber is applied (or "laid up," as this part of the process is referred to as "lay up"). In Munich, we saw robots being used to lay up carbon fiber strips along the surface of a large foam form, but there are plenty of other ways. In fact, while simple symmetrical carbon fiber parts can easily be created by mechanical means, it’s not uncommon to have large and complex asymmetrical carbon fiber parts being laid up by hand.

But carbon fiber isn’t carbon fiber without the glue. The methods for introducing the epoxy material used to bind the threads into shape vary—for our Munich trip, for example, the automated fiber placement robot used carbon fiber threads pre-impregnated with epoxy. The threads came from long spools which had to be kept chilled to prevent the epoxy from curing, and as they were applied by the robot to the mold surface, the robot head itself heated the threads to spot-cure them.
There are tons of other methods to get glue into the works. For super high-strength parts like you’d find in a race car, sheets of cut carbon cloth are placed into molds and then epoxy is injected into them. Other times, a carbon fiber part is actually painted (like, actual brushes) with epoxy after being laid up over a mold.
Regardless of the epoxy application, the carbon fiber part doesn’t really become a true composite part until it’s cured. That’s a chemical process brought about by a number of ways—most often by heat, though there are epoxies that cure best in vacuum or under pressure or even just by being left alone in room temperature. The result is just like regular glue hardening, except here the resin is providing a stiffening, cross-linked matrix that rigidizes the carbon threads. Additionally, the carbon fiber threads themselves undergo chemical changes during curing, expelling non-carbon molecules that were present in the pre-thread material and creating stronger bonds between the actual carbon atoms. The resulting composite material is what we commonly refer to as "carbon fiber"—a dark-colored stiff material with a fabric-like visual appearance. That fabric is the woven carbon fibers themselves.
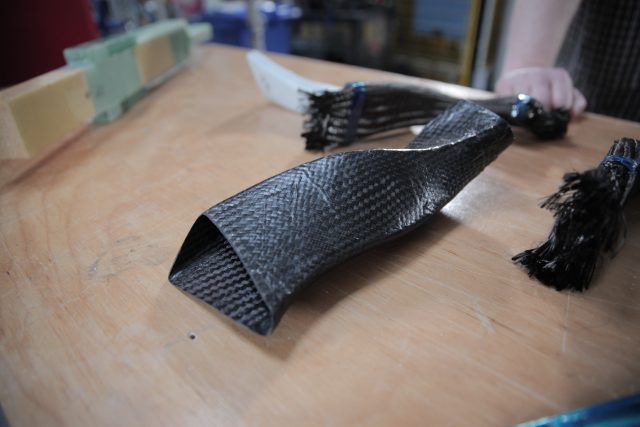
reader comments
173